How to Repair Common Laminate Flooring Problems
Whether the laminate flooring in your home has been there since before you moved in or you recently installed it yourself, you want to keep it in good shape. Unfortunately, problems do come up sometimes. The good news is that in many cases, you can fix the problem without replacing the entire room’s floorboards. Check out a step-by-step guide in how to repair laminate flooring in the three most common areas.
How to Repair Laminate Flooring: Peaking
If you’ve noticed that the floorboards are pushing up against each other along the seams, creating a lump on the floor that resembles a roof’s peak, the problem is peaking. Peaking occurs when the floorboards don’t have enough space to expand and contract.
To avoid further damage, you should fix the problem as soon as possible.
Find the Underlying Laminate Flooring Problem
Peaking commonly happens when there isn’t an expansion gap between the floor and the walls, when the expansion gap is too small, or if the moldings are attached to the laminate flooring. To find the underlying issue:
- Follow the peaking boards to the nearest wall.
- Check for a gap between the board and the wall or any nearby permanent fixture such as cabinets. A 0.25-inch gap usually provides enough space.
- Check the moldings for any nails or glue that may have attached them to the floorboards.
Fix the Underlying Laminate Flooring Problem
If the moldings are attached to the floorboards, remove the nails or detach the glue.
If the floor doesn’t have an adequate expansion gap, you’ll have to make one. Simply remove the molding and cut a section of flooring between the floor and the walls. Helpful tools include spacers and a jigsaw. Replace the molding. Finished!
Fix the Peaked Boards
The peaking is the main issue. Once you’ve corrected the underlying problem, you can place a heavy object on the peak for a few days or until the boards settle back into place.
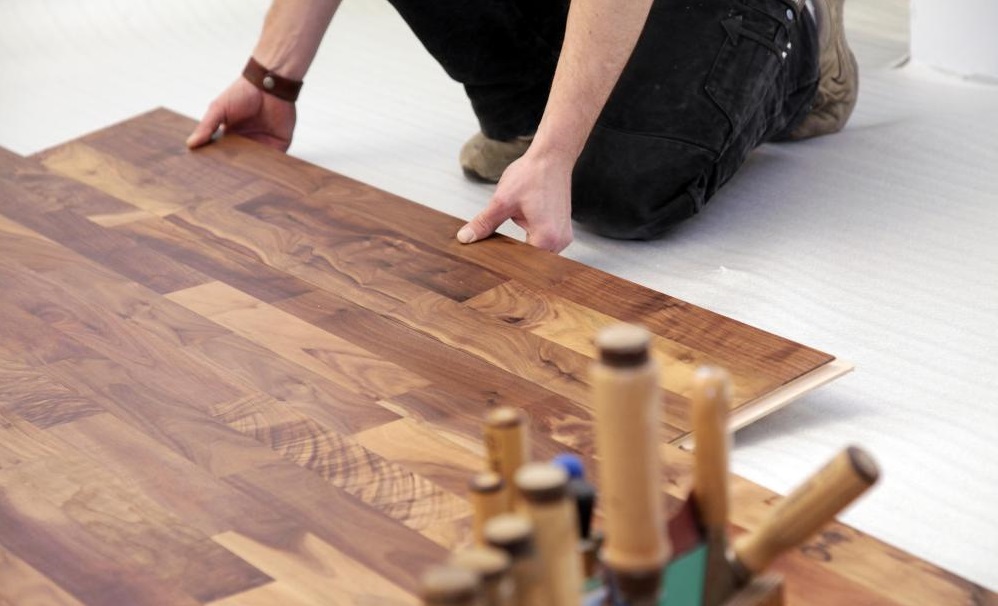
How to repair water damage to laminate floors?
A laminate flooring generally is resistant to water damage, however, it still faces damage due to excess of moisture. But the good thing about laminate floors is that the water damage can be repaired easily without peeling the entire floor. This is because the flooring type is made of many sections that are locked together.
Here we will be discussing about repairing the water damage and drying the floor underneath, which form the part of the cleaning process. And the final step calls for putting down the new laminate in place of the section that is damaged.
Repairing and drying the laminate floors
In most of the cases, laminate floors get flooded when there is a leakage in a dishwasher, refrigerator or washing machine. Other than these, any standing water can cause the damage. The very first thing you have to do is determining the place of damage and fixing it. Once this is done, the floor must be dried well. You can complete the task by mopping or by using a wet-dry vacuum. After drying the excess of water, a fan must be placed on the floor to dry the floorboards beneath before repairing the damaged sections.
You can make use of a circular saw or crowbar to fix the water damage by removing the wet sections. Using a chisel and hammer, start pulling the damaged pieces, ensuring all the while that the surrounding area is not ruined. Next the tongue part of the laminate board must be removed with the help of a knife. After removing the old laminate, put a fan on the floorboards to dry them. This must be done before you add the new material as it will prevent molds from growing in future as a result of moist floorboards.
Putting new laminate
Before putting the new laminate down, create a pattern matching the current flooring. Thereafter construction glue must be added. Then you must place the first piece into the right area as per the pattern. Make sure that you wipe off any extra glue before the area dries, and place heavy objects only when it’s fully dry. If you are willing to use nails instead of glue to repair the water damage laminate floors, you will first have to nail the first section of the new floorboard with the existing sections so that it fits compactly.
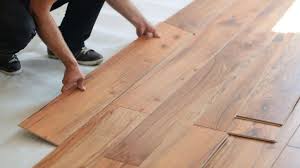
How to Repair Laminate Flooring: Creaking Floors
While occasional creaks and groans are normal — especially in older homes — regular noises are annoying and may indicate an issue with the floor. You’ll need to assess the situation and determine if you can fix it yourself or if you require professional help.
- Check Transition Areas
Unless your home has the same laminate flooring in every connecting room, you’ll find transition areas where the floorboards meet another type of flooring such as carpet, tile, or linoleum. Look for transition strips — long, thin pieces of metal or wood — that connect one area to the next. Ideally, your floor should have them.
If there aren’t any T strips, look for expansion gaps in the connecting areas. As with walls and stationary objects, laminate flooring needs space to expand and contract here. If you don’t see a gap, you’ll need to make one, as outlined above, and then install a T strip.
- Pull Up The Floor
Check for problems beneath the surface by pulling up a board or two. Is there an underlayment pad between the subfloor and the laminate flooring? If not, you can fix or at least mitigate the creaking noises by uninstalling the floorboards, adding a high-quality underlayment pad, and reinstalling the boards. This item absorbs sound and adds durability to your flooring.
- Examine the Subfloor
Another possible issue is an uneven or damaged subfloor. Look for dips and humps in the floor or areas that feel spongy. Make sure to check underneath any rugs or furniture, too. If you suspect that your subfloor is rotting or uneven, you should contact a flooring professional.
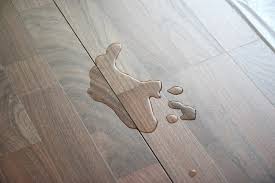
How to Repair Laminate Flooring: Buckling or Warping
You’ll know that you have warped floorboards if they curve inwards like the inside of a bowl. Buckling is the opposite — when floorboards resemble an arch or an upside-down bowl. Water damage or temperature fluctuations are the most common culprits of buckling and warping. If you address the issue quickly enough, you can usually prevent the laminate flooring problems from spreading.
Look For Water Damage
Causes of water damage include:
- Standing water. It may come from a plumbing leak, an overflowed dishwasher, or from mopping with too much water.
- High humidity.
- Moisture from the subfloor.
The first two sources are easy enough to diagnose. To check your subfloor, pull up the floorboards and look for moisture or signs of mold. Also, check for an underlayment pad; not having one makes your laminate flooring susceptible to moisture damage.
Look for Expansion Gaps
Not having proper expansion gaps can cause not just peaking and creaking floors, but buckling and warping floorboards too. If most of the damage is near the walls, your problem is likely due to one of the following installation mistakes:
- Not acclimating the flooring to the home before installation.
- Not leaving an expansion gap between the floorboards and the walls, stationary objects, or transition areas.
In either case, creating expansion gaps should fix the issue.
Fix the Underlying Cause
Before you replace the damaged floorboards, you’ll need to fix the underlying cause. This task may involve:
- Taking care of any plumbing issues.
- Purchasing an underlayment pad.
- Creating expansion gaps.
- Purchasing higher-quality flooring that has a strong moisture barrier. While this step isn’t necessary, you may want to consider it if you have cheap, low-quality flooring that lacks a proper moisture barrier.
Replace the Damaged Floorboards
You’ve almost finished the job! Just follow these last steps:
- Locate the closest wall and remove the molding.
- Disconnect and remove all the planks until you reach the damaged section.
- If there’s water damage, allow the area to dry completely.
- Deal with any mold on the subfloor. Contacting a mold removal specialist is a good idea.
- When the subfloor is dry and clean, you can install the replacement floorboards.
- Reinstall the laminate flooring.
- Reattach the molding.
You don’t need to completely uninstall the flooring unless the damage is extensive or if you want to add higher-quality floorboards or underlayment. If you have damaged laminate floorboards in the middle of a large room, you may prefer to hire a flooring professional.
Deciding Between Hardwood and Laminate Flooring: Which Is Better?
When investing in a new floor, many homeowners are faced with a choice between hardwood and laminate. The difference between these two types of floors can be confusing at first, which is why we put together a simple guide that compares hardwood against laminate, highlighting the pros and cons of each floor type in terms of appearance, durability, longevity, ease of maintenance and repair, and eco-friendliness.
The Fundamentals
Laminate is a multi-layer synthetic flooring product. It is designed to imitate the appearance of real wood. The core layer of laminate flooring is manufactured primarily from melamine resin and fiber board material. The top layer has an imprinted textured image made to look like real wood.
Engineered hardwood flooring is a type of wood floor that consists of several wood or plywood layers. Bottom and middle layers are manufactured from cross-laid solid wood or plywood planks. The top layer consists of a solid sawn wood lamella, often stained and prefinished in factory setting. Solid hardwood flooring planks are produced from single pieces of wood, can be purchased unfinished or prefinished.
In essence, while solid or engineered hardwood flooring is manufactured from real wood and preserves the unique textured grain and appearance of natural wood, laminate flooring is only an imitation. Although some types of high quality laminate floors might look like real wood, there are far more differences between these products than what initially meets the eye.
Appearance and Aesthetics
In terms of aesthetics, the difference between hardwood and laminate floors is glaringly obvious. Real wood is characterized by tremendous texture variation of the wood grain, which is why no two planks of hardwood flooring, whether solid or engineered, appear exactly alike. In laminate flooring, pre-designed patterns that imitate the look of wood texture, are imprinted onto the floor surface. For this reason, identical patterns are repeated on average every 5 boards.
Although in appearance some high quality laminate floors may look like real wood, repetition is unavoidable, as uniqueness of an authentic wood is impossible to replicate.
Durability
Durability of any flooring surface largely depends on intensity of foot traffic, as well as adherence to manufacturer recommendations in regards to care and maintenance of the floor.
Outer layer of most laminate floors is manufactured by bounding melamine resins and aluminum oxide at high heat and extreme pressure. The resulting floor surface is often harder than that of natural wood. Most laminate floor surfaces are highly resistant to moisture damage, staining and fading. In fact, many reputable laminate flooring manufacturers offer 10 to 25 year warranties on finish.
Durability of an authentic hardwood floor varies depending on finish, manufacturer and maintenance practices. Natural wood is softer than a pressurized composite surface, therefore, it can dent more easily. Solid or engineered hardwood floors can be refinished, renewed and repaired fairly easily, often without the need to replace planks or even the entire floor, as is the case with damaged laminate flooring. For example, in the event that an oiled wood floor plank is damaged, it can be fixed by manually sanding down the affected area, then simply applying more stain and oil. With laminate flooring, simple DIY spot repairs are not possible.
On some types of hardwood floors, such as those with wire brushed and oiled finishes, minor surface dents and scratches seamlessly blend in with the existing look, emphasizing the unique appearance and depth of wood texture. Once scratched or chipped, laminate flooring surfaces will show the damage.
Moisture
Wood is an organic, “breathing” material that responds to fluctuations in humidity and temperature. For this reason, solid and engineered hardwood floors should be installed in interiors where humidity levels are monitored and kept at 45-55% for solid and 45-65% for engineered floors. Although engineered hardwood floors have superior dimensional stability, most wood floor manufacturers do not recommend installing them in bathrooms or kitchens – areas, where temperature and humidity can fluctuate significantly. In warm and humid climates, such as Florida, hardwood flooring that is multilayer or engineered is preferable over solid.
Laminate floors have high resistance to moisture and are often used for kitchens, bathrooms, and basements. Nevertheless, it’s important to carefully read the manufacturer warranty and recommendations in order to avoid costly mistakes.